摘要:激光焊機(jī)在冷連軋機(jī)組中作用十分重要,是保證連續(xù)軋制的前提。激光焊機(jī)焊接質(zhì)量的穩(wěn)定決定了機(jī)組運(yùn)行的穩(wěn)定。通過(guò)對(duì)冷軋1550mm機(jī)組生產(chǎn)時(shí)焊縫處斷帶進(jìn)行分析影響焊縫因素,總結(jié)影響焊縫質(zhì)量的主要因素以及改進(jìn)和應(yīng)對(duì)措施。前言
安鋼冷軋酸軋機(jī)組1550mm酸軋機(jī)組設(shè)計(jì)年生產(chǎn)能力120萬(wàn)t,產(chǎn)品規(guī)格為0.25mm~2.0mm×800mm~1430mm,焊接工藝采用TMEIC激光焊機(jī)。激光焊接熱軋鋼帶具有對(duì)接焊縫牢固,軋制中動(dòng)態(tài)厚度超差長(zhǎng)度較短,軋機(jī)斷帶風(fēng)險(xiǎn)低等優(yōu)勢(shì)。TMEIC激光焊機(jī)布置在酸洗軋機(jī)聯(lián)合機(jī)組入口段,位于液壓雙切剪之后,1#和2#張力輥之前。焊接原理為深熔焊接,即將高強(qiáng)度的激光束輻射至連接帶鋼表面,使金屬熔化實(shí)現(xiàn)帶鋼的連接。激光焊機(jī)主要由激光源、焊機(jī)入口部分、焊機(jī)本體、焊機(jī)出口部分、月牙剪、氣站和電氣控制部分組成。激光源為德國(guó)通快(TRUMPF) 公司生產(chǎn)的軸流式CO2連續(xù)激光源。1、激光焊機(jī)生產(chǎn)現(xiàn)狀在酸軋機(jī)組正式投產(chǎn)的一年內(nèi),因激光焊機(jī)焊縫質(zhì)量問(wèn)題造成焊縫在拉矯機(jī)處斷帶兩次,每次事故處理時(shí)間均在8h以上,且處理焊縫斷帶事故后,焊縫前后各一百多米帶鋼不能進(jìn)行軋制,造成熱軋?jiān)侠速M(fèi)約6t。因激光焊機(jī)焊縫質(zhì)量問(wèn)題造成焊縫在軋機(jī)處斷帶約20次,每次處理時(shí)間大約為1h,造成廢鋼量為1t,同時(shí)對(duì)軋輥造成嚴(yán)重?fù)p傷,斷帶率約為0.365%。焊縫處斷帶對(duì)生產(chǎn)造成影響較大,機(jī)組停車(chē)時(shí)間長(zhǎng),產(chǎn)生廢品多,對(duì)軋輥和設(shè)備產(chǎn)生危害大,造成生產(chǎn)成本高和機(jī)組效率低,因此減少或杜絕焊縫處斷帶十分重要。
2 、焊縫斷帶原因分析
2.1、焊縫在拉矯機(jī)處第一次斷帶原因分析第一次兩卷厚度為3mm焊縫在矯直機(jī)處拉斷,帶尾甩到酸槽,帶頭掉入活套第三層中部。斷帶為DS側(cè)開(kāi)裂撕向WS側(cè),DS側(cè)位置斷口整齊,斷面光滑為剪切斷面,具體如圖1所示。
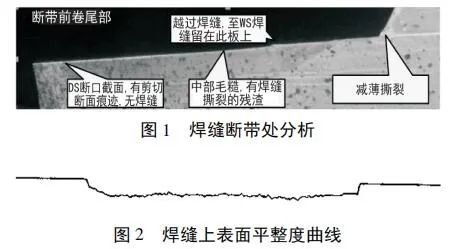
從圖2可以看出,上表面焊縫DS側(cè)起始高度正常,之后短距離迅速下降,一直接近下限,至WS側(cè)30cm左右上升至正常水平。因此,根據(jù)斷帶處的樣貌和焊縫平整度曲線分析可以得出: 假定焊槍軌道為一條直線,形成焊縫為一條直線,用實(shí)線表示; 而實(shí)際頭尾剪切對(duì)接后,形成的縫隙為切縫,用虛線表示; 二者的相對(duì)位置如圖3所示。在過(guò)拉矯機(jī)時(shí),有一定的延伸率,DS側(cè)實(shí)際未熔合,造成開(kāi)裂。
2.2、焊縫在拉矯機(jī)處第二次斷帶原因分析
第二次拉矯機(jī)處發(fā)生斷帶,帶尾甩過(guò)4#張力輥,帶頭掉在入口活套上升過(guò)道上。斷帶為過(guò)拉矯機(jī)時(shí)中部開(kāi)裂,彎曲時(shí)撞向上矯直輥形成褶皺,無(wú)法咬入拉裂帶鋼,中部斷口整齊無(wú)明顯斷口,向WS側(cè)和DS側(cè)越發(fā)毛糙,最終在距WS側(cè)和DS側(cè)15cm處越過(guò)焊縫,形成拉裂,斷面減薄明顯,如圖4所示。

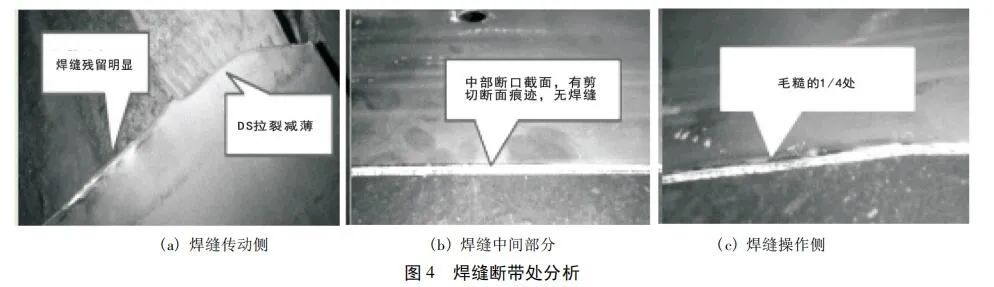

根據(jù)焊縫平整度曲線( 如圖5所示) ,可以看出焊縫自兩邊向中間焊縫高度逐漸降低,之后略有上升中間出現(xiàn)尖峰,此點(diǎn)為異常值,與焊縫中部的毛刺有關(guān)系。因此根據(jù)斷帶處的樣貌和焊縫平整度曲線分析可以得出: 假定焊機(jī)軌道為一條直線,形成焊縫為一條直線,用實(shí)線表示; 而實(shí)際頭尾剪切對(duì)接后,形成的縫隙為切縫,用虛線表示; 二者相對(duì)位置如圖6所示。在過(guò)拉矯機(jī)時(shí),有一定的延伸率,中間焊縫未焊實(shí),中間位置首先開(kāi)裂,彎曲時(shí)卡鋼造成帶鋼撕裂斷帶。
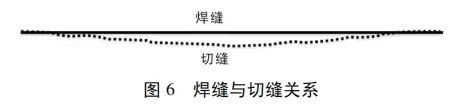
兩次發(fā)生斷帶位置均為拉矯機(jī)處,發(fā)生原因也相似。因此通過(guò)焊機(jī)的打點(diǎn)測(cè)試確定激光和切縫的相對(duì)位置關(guān)系,經(jīng)過(guò)測(cè)試發(fā)現(xiàn)切縫與激光點(diǎn)位置相對(duì)關(guān)系,如圖7所示。
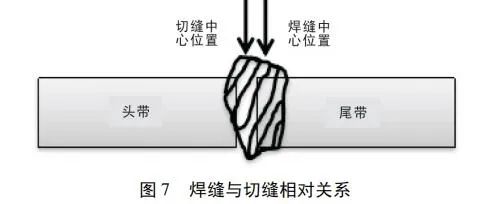
切縫與焊縫位置不一致,由于切縫設(shè)置為0,焊縫寬度又很窄,肉眼和跟蹤缺陷上有時(shí)很難看的出來(lái),容易造成誤判,因此這兩次焊縫處的斷帶均屬于切縫質(zhì)量不好,且激光位置與切縫存在誤差,導(dǎo)致焊縫在切縫質(zhì)量不好的地方造成焊接質(zhì)量下降,在遇到拉矯延伸時(shí)造成開(kāi)裂,最終形成焊縫處斷帶。2.3 、焊縫在拉矯機(jī)處斷帶原因分析從現(xiàn)場(chǎng)當(dāng)時(shí)帶頭尾剪切情況分析,斷帶的前后兩卷的頭尾剪切量都小于2m,說(shuō)明頭尾的板形不良影響了焊縫質(zhì)量,同時(shí)這兩次斷帶焊縫的切月牙均未投入使用,從現(xiàn)場(chǎng)的斷帶樣貌看,焊縫邊部質(zhì)量不好,熱軋頭尾軋制過(guò)程中屬于無(wú)張力軋制,頭尾展寬相對(duì)較大,因此在頭尾焊接時(shí),雖然鋼卷規(guī)格相同但頭尾的寬度存在差異,焊縫邊部屬于焊接應(yīng)力集中區(qū),在受到拉矯延伸時(shí)易開(kāi)裂。因此,造成兩次斷帶的情況可以總結(jié)為以下幾種原因:
(1)帶鋼頭尾板形不好;
(2)焊機(jī)剪刃剪切帶鋼質(zhì)量不好;
(3)焊機(jī)激光焦點(diǎn)位置的偏離;
(4)焊縫兩端沒(méi)有剪切月牙。
3、 焊縫質(zhì)量改進(jìn)措施
(1) 根據(jù)現(xiàn)場(chǎng)操作情況和設(shè)備情況,針對(duì)焊縫的質(zhì)量制定了檢測(cè)方法,具體方法見(jiàn)表1。(2) 焊縫質(zhì)量的不穩(wěn)定,板形的原因可能性最大,焊機(jī)操作工需要根據(jù)焊縫質(zhì)量和頭尾板形對(duì)焊縫兩端進(jìn)行剪切月牙,焊縫兩邊剪切月牙以消除焊縫應(yīng)力集中區(qū)。(3) 對(duì)于板形造成的困擾,可以設(shè)定0.1mm焊縫,同時(shí)填充焊絲,對(duì)防止有浪處的擠壓和改善焊縫強(qiáng)度有作用。(4) 增加焦距可適當(dāng)增加帶鋼上表面光斑,加寬焊縫寬度,減輕偏差造成的影響。
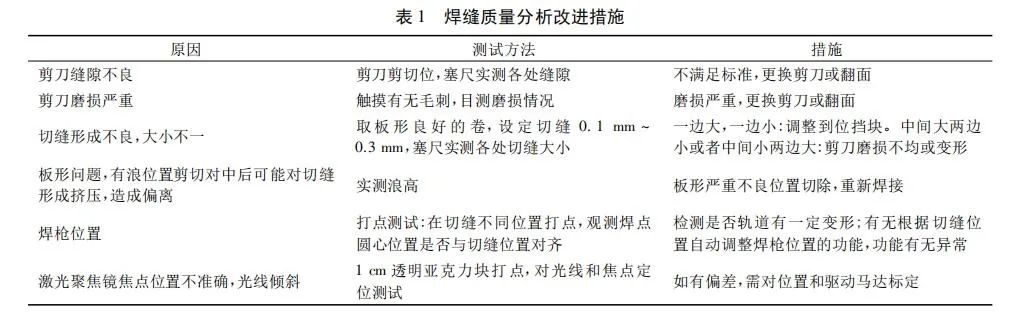
4、 改進(jìn)效果通過(guò)對(duì)冷軋?jiān)腺|(zhì)量改善
定期對(duì)焊機(jī)設(shè)備根據(jù)表1進(jìn)行點(diǎn)檢,維護(hù)焊機(jī)焊接質(zhì)量的穩(wěn)定,在降低焊機(jī)重焊率的同時(shí),杜絕了由焊縫質(zhì)量造成的焊縫處斷帶,在經(jīng)濟(jì)方面為機(jī)組的節(jié)能降本提供了保障,在運(yùn)行效率上機(jī)組實(shí)現(xiàn)了高效穩(wěn)定運(yùn)行。
5、結(jié)語(yǔ)
通過(guò)對(duì)焊縫斷帶處的分析和改進(jìn),提高了焊機(jī)的操作和維護(hù)能力,杜絕了焊縫處的斷帶,為機(jī)組穩(wěn)定高效運(yùn)行提供了保障。焊縫質(zhì)量的穩(wěn)定降低了廢品量,減少停機(jī)時(shí)間,機(jī)組運(yùn)行成本也相應(yīng)降低。